How Crystal is made in Nuovacev
Lalique
Relief work (Lalique type) is one of the most interesting characteristics of our production, as well as milling resulting in miniature-like patterns which can hardly be rivalled. A master craftsman with over forty years of expertise turns his craft into art and calls into being a mixture of painting and bas-relief on a hard and shining surface.

Presently, the workpiece is polished with both sulphuric and hydrofluoric acid, and is then assembled in case it is made of different parts (this stage is called bonding). The workpiece is then engraved through sand-jet treatment in order to avoid forgery, and is eventually packed and dispatched.
The hardest part of the job is the very last, and has nothing to do with crystal production – it is getting paid for it…!
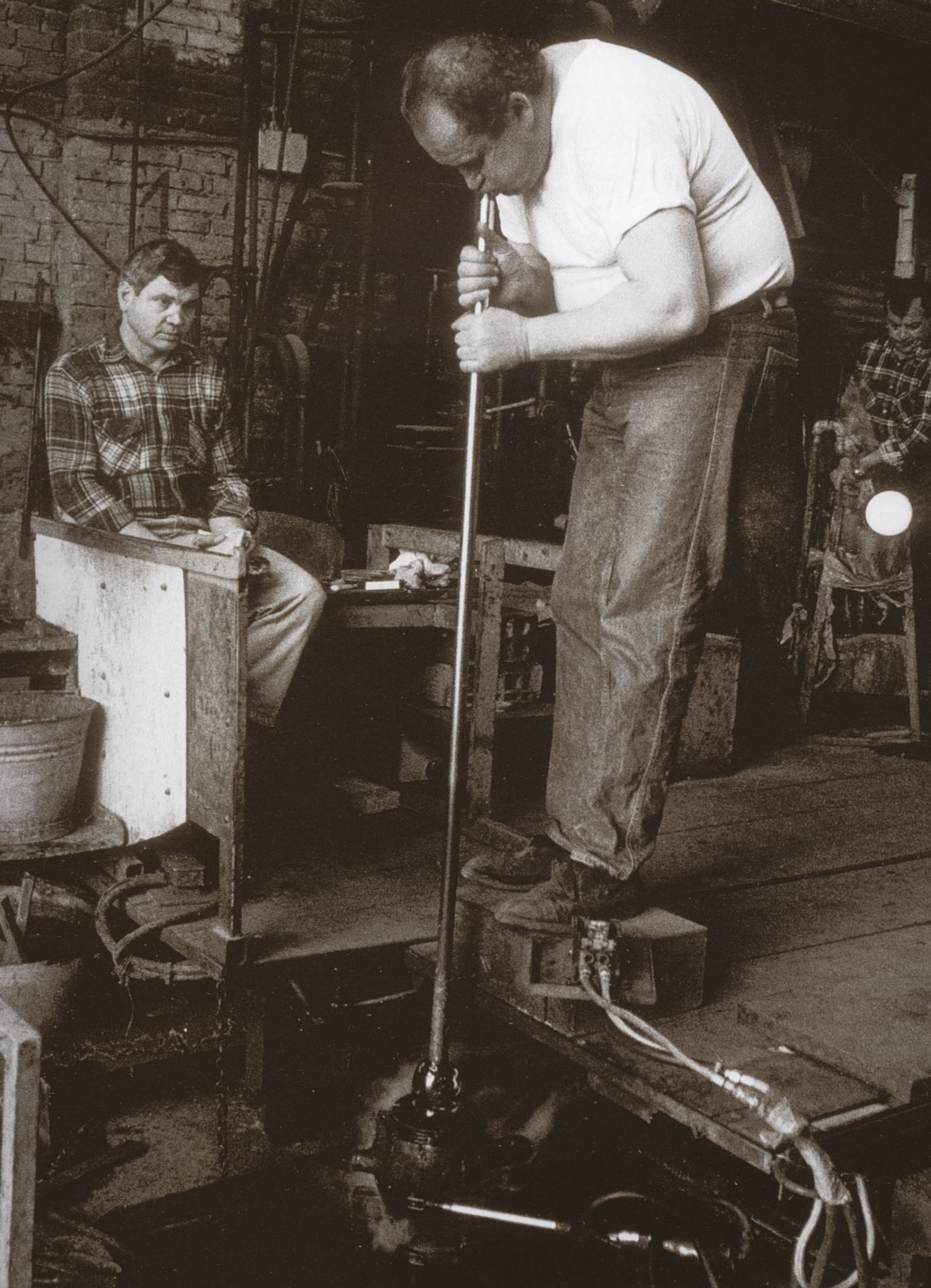
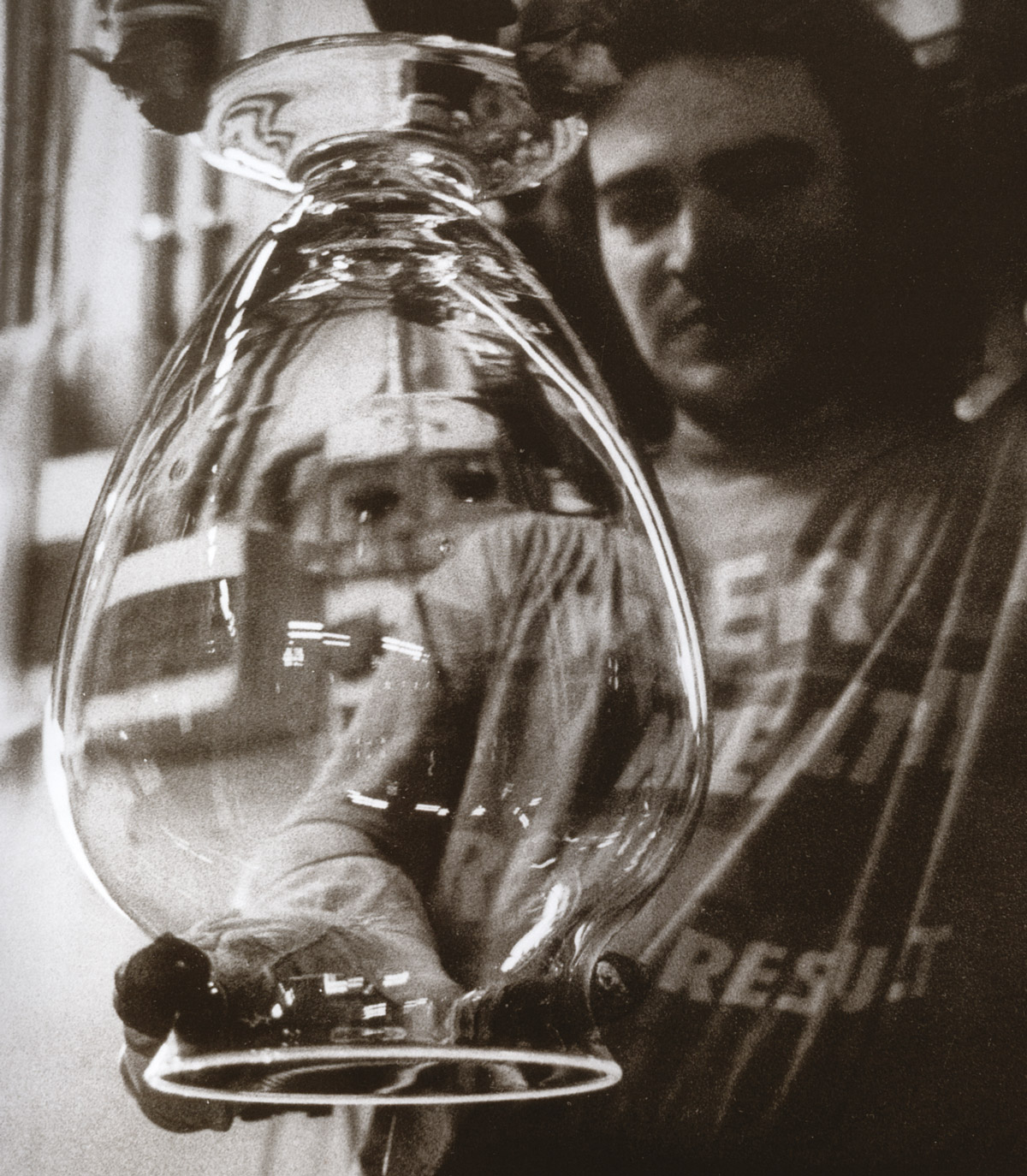

This is the recipe
Take a firm with melting furnaces whose temperature can reach 1400° C, and put into them a mixture (with secret dosage) of silica, lead oxide, sodium carbonate, potassium carbonate, potassium nitrate, pentahydrated borax, antimony trioxide, and other secret ingredients. After some hours of sweating on the part of the casting workers, transparent crystal is ready to be manufactured. If you want it blue, add cobalt oxide to the mixture. If you like it green, add potassium dichromate. If you like it ruby red, just throw in some of your family’s gold.
Manufacturing techniques
Let the mixture rest for some while until the glassworkers come along with their steel gathering pipes. The mixture is now at an average temperature of 1200° C which keeps it semi-liquid. The glassworkers will extract small quantities of the mixture and will start manufacturing it according to one of the following techniques:
- A. press and/or injection: crystal is cast in a mould where a male plug will push and press it against the mould’s walls
- B. blowing: same procedure as above, but crystal is pressed against the mould’s walls by the air from the lungs of the blower
- C. hand-made: the master glassworker creates the workpiece by using scissors, hooks, compasses, and other small tools of his own invention
Similar but never identical Crystals
Clearly, workpieces manufactured according to A) and B) above will have their shape determined by the mould, even though their thickness, weight, and glass separation varies according to the glassworker. Workpieces manufactured according to C) above, on the other hand, are similar but never identical.
A variation can be introduced in techniques B) and C) above in order to obtain the so-called case glass (or verre double, as the French would say), whose manufacturing process is extremely complex and whose secret is jealously guarded by glassworkers. The only thing which can be revealed is that it can be referred to as double work, since it involves heat lamination of two crystal types of different colours.
Glassworkers are organised in groups (called circles) within which each worker has a specific role. The circle leader co-ordinates the whole team who work together in order to manufacture the same workpiece.
Cold working
After hot working, the workpiece is placed on a conveyor and into a pre-heated tunnel called “tempering tunnel”. The temperature of the first part of the tunnel reaches about 600° C and will decrease down to ambient temperature in about four hours.
Usually, in most factories the workpiece is ready for delivery and sale upon exiting the tempering tunnel. In our case, though, the workpiece must still undergo strict quality controls as well as further transformation through the so-called cold working, i.e. glass stoning, polishing, sandblasting, and bonding.
It is the task of edge finishers to cut, band-saw, and polish the workpiece during finishing. On a second time, master engravers will use diamond grinding wheels to decorate and panel the workpiece so that the polish and ductility of crystal are highlighted. This is possible thanks to the lead oxide present in crystal allowing for light refraction which possesses many of the optical properties of diamond. Furthermore, the workpiece has such malleability so that it can be easily engraved (whereas glass can not).